Drilling hard brass castings
Drilling a hole into a hard brass casting can be frustrating. Your finished model will benefit as it will be stronger and more resilient to handling.
Firstly I heat the castings with a flame until the casting turns cherry red. Allow to naturally air cool, this somewhat softens the brass and makes a difference when drilling. I use the Jaycar Torch TS1660. It has a piezo ignition and has proven to be reliable with the ones I have bought lasting well over 3 Years, with almost daily use. I’ve had just one piezo crystal break, I’m ok with that. I have no affiliation with Jaycar, I am a satisfied end user only.
I chuck my drill bits very short, only leave enough drill bit out to clear the hole depth. These little fella’s often break just by looking at them, having a few spare is prudent I feel. I lubricate with bar soap (or beeswax). I would only consider using HSS drill bits in brass. Double check the casting you are about to drill is flat at that point. If it appears rounded, give the casting a quick light file, you may find it hard to start the hole otherwise.
Take your time, back the drill bit out at regular intervals. Before long the drill will poke out the other side. It’s at about this point my hand becomes completely cramped up, and if I push on to another hole immediately, I usually break a drill bit. I’ll wait a sec before drilling the next hole.



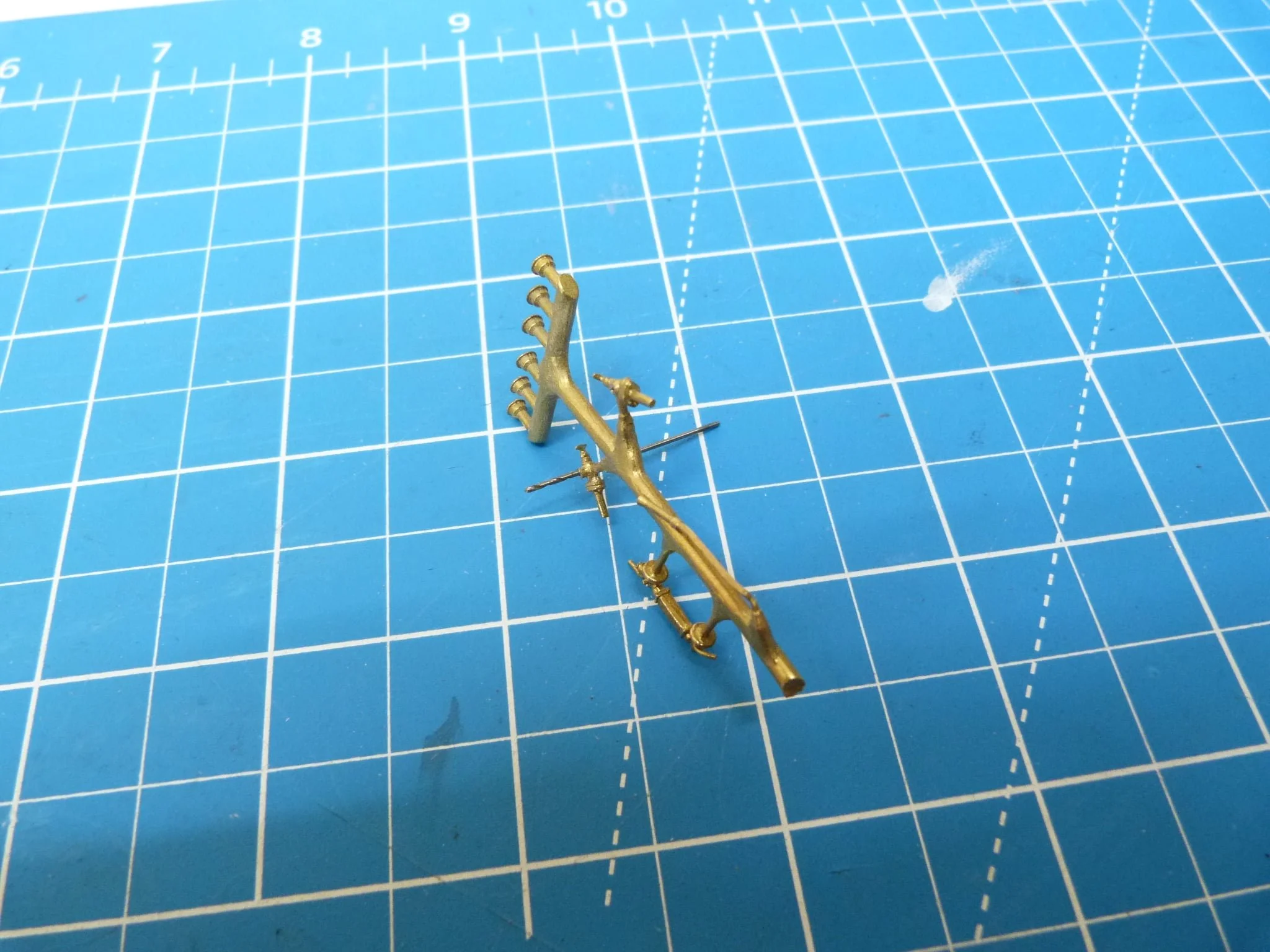
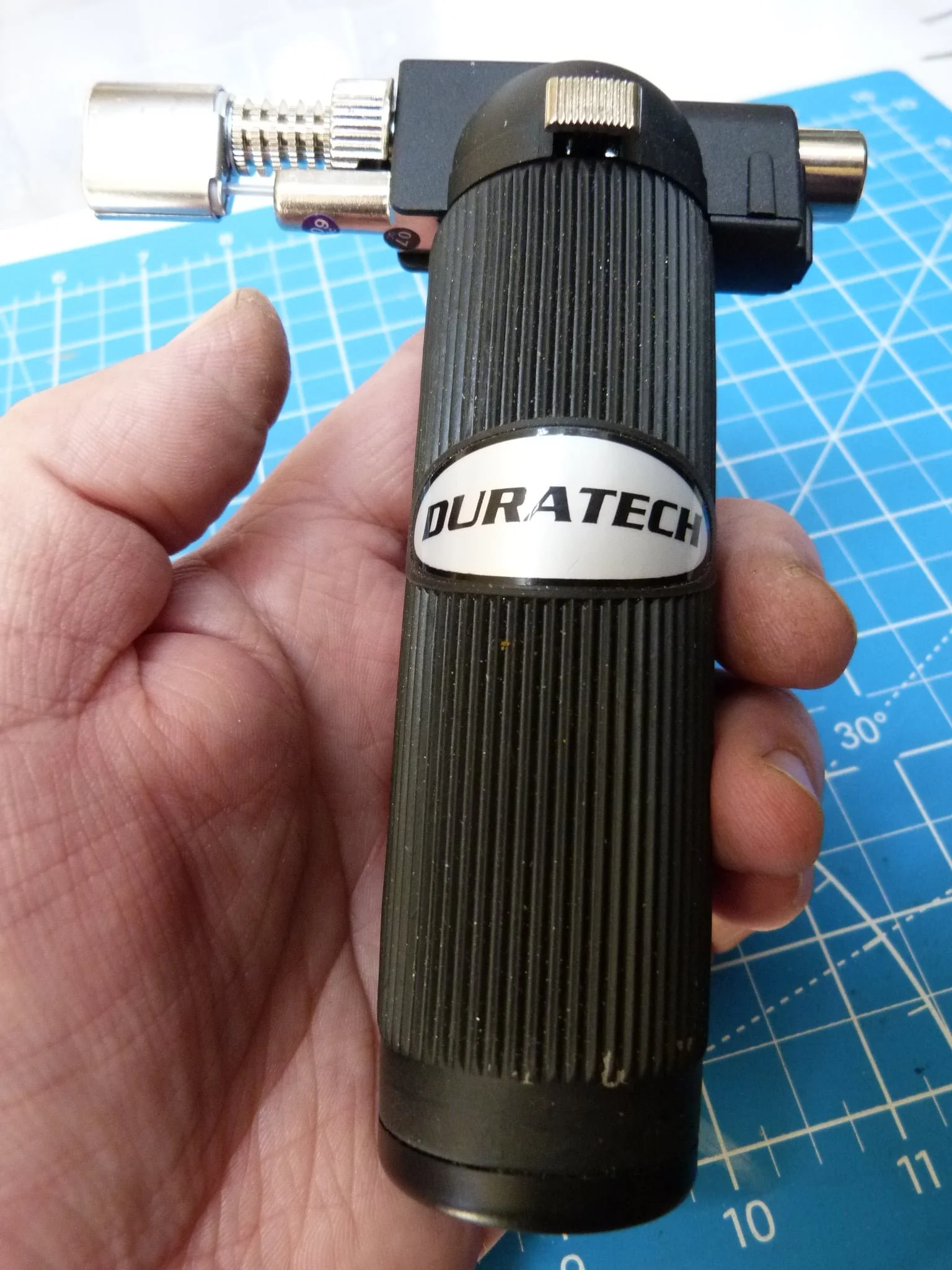